Keynote
Usability engineering, design for manufacturing or circular design?
"Design for manufacturing and sustainability go together perfectly!"
Frank Detering is head of our office in Stuttgart and a qualified designer and process engineer
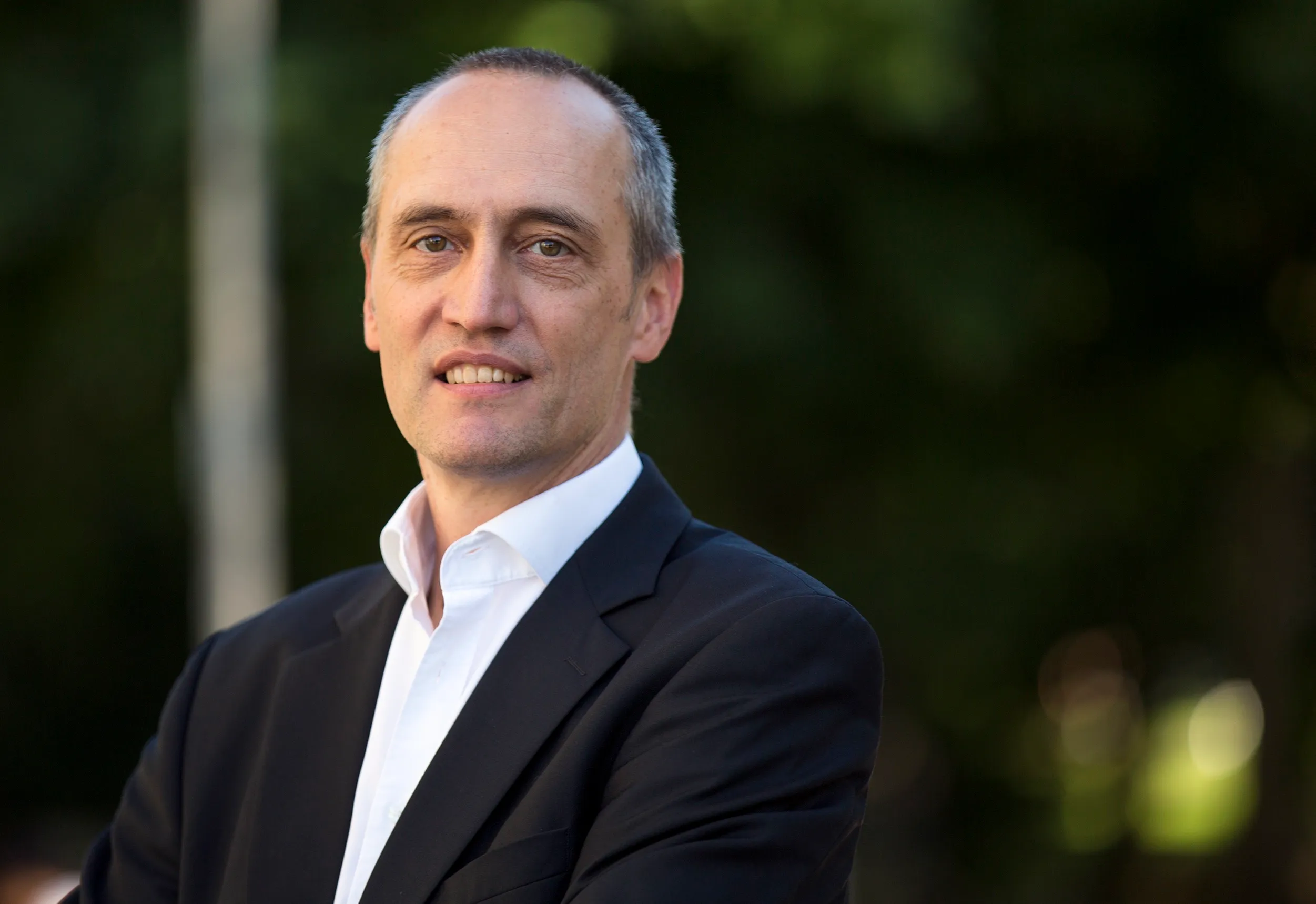
Theimmense importance of usability in the development of products - and medical devices in particular - has been undisputed for many years and the number of articles dealing with the best test methods and procedures for determining usability and user needs is huge. With Design For Manufacturing, or DFM for short, the focus is not on the user but on the manufacturer, or more precisely on the manufacturing processes. On closer inspection, the two methods can be compared to tunnel construction, where miners dig through the mountain from two sides to meet in the middle. The main aim here is to reduce costs by shortening the processing time.
In the 1970s, Geoffrey Boothroyd conducted initial research at the University of Massachusetts to provide developers with tools for use in automated manufacturing processes. The aim of this research was
- the reduction of assembly processes due to fewer components
- the simplification of assembly processes
This was new, because until then the common goal of developers had been to design all individual parts as simply as possible in order to reduce production costs. And here someone developed tools to save money in production with a smaller number but more complicated components, because assembly was easier and faster. Together with Peter Dewhurst, the software "Design for Automatic and Manual Assembly" (DFA) for the Apple II was launched and, after initial successes, BOOTHROYD DEWHURST Inc. - what a tongue twister - was founded in 1983, which to this day sells software that is used by major manufacturers (Ford, General Motors, John Deere, etc.) in particular.
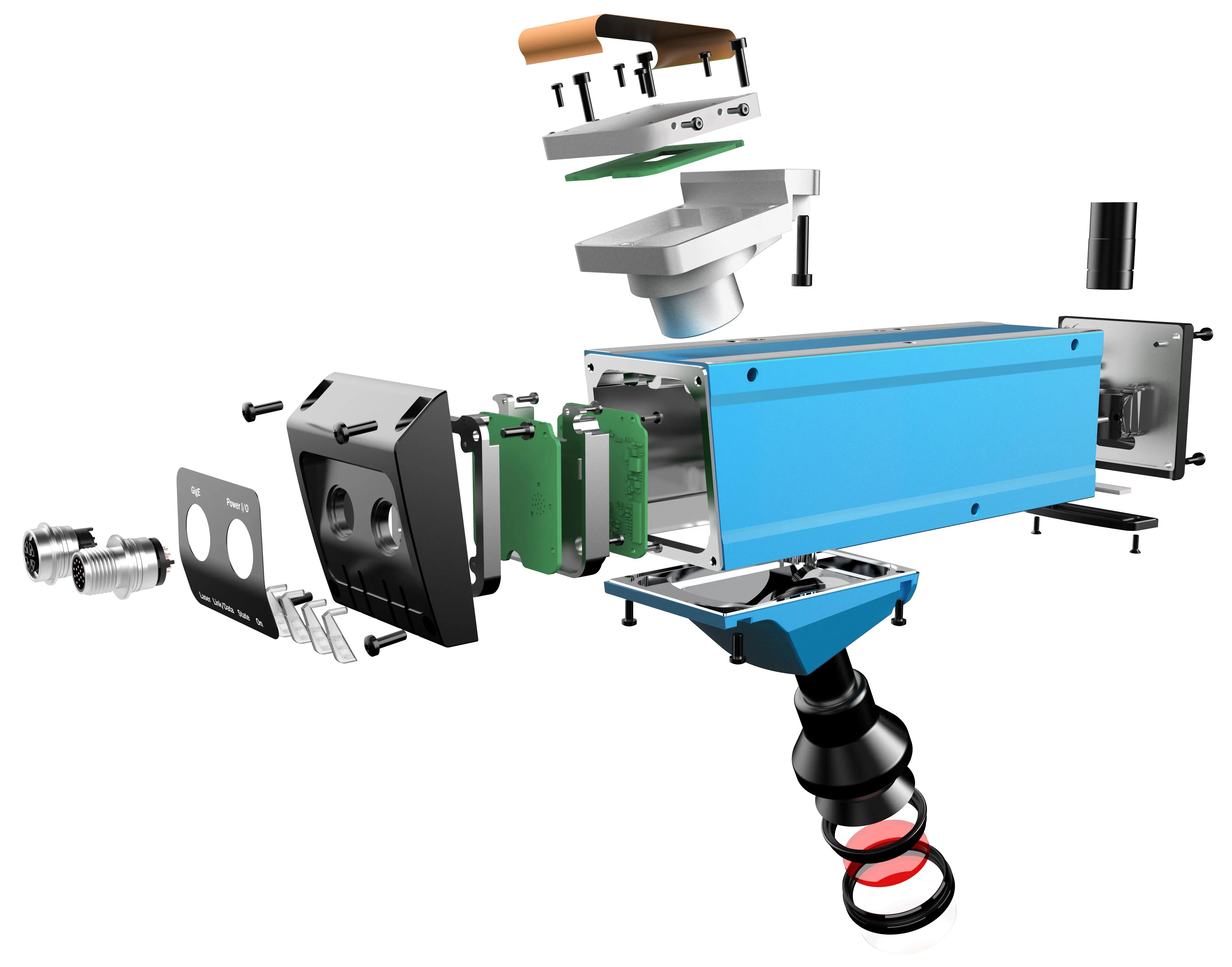
What is important in Design for Manufacturing?
The know-how and experience of the developers play a decisive role in DFM, as around 80% of the product costs are already determined in the development phase. The following criteria are considered:
1. material selection: Taking into account the manufacturing possibilities, designers can select materials that can be processed well and at the same time fulfill the desired properties of the product.
2. production processes: DFM takes into account the various production processes and technologies used for manufacturing. By optimizing the design of the product, unnecessary steps or complex procedures can often be avoided.
3. assembly: DFM aims to make the assembly of the product as simple as possible. This can be achieved by designing components with simple joining techniques, clear assembly instructions and the use of standardized fasteners. This leads to shorter lead times and lower costs.
4. error and scrap minimization: Design decisions are made in such a way that they reduce the risk of errors and rejects, e.g. by adjusting tolerances so that components fit together more easily or by changing design elements in such a way that the probability of errors during production is reduced.
5. cost optimization: The modular design of products allows identical parts to be produced, which can be manufactured in higher quantities at lower cost.
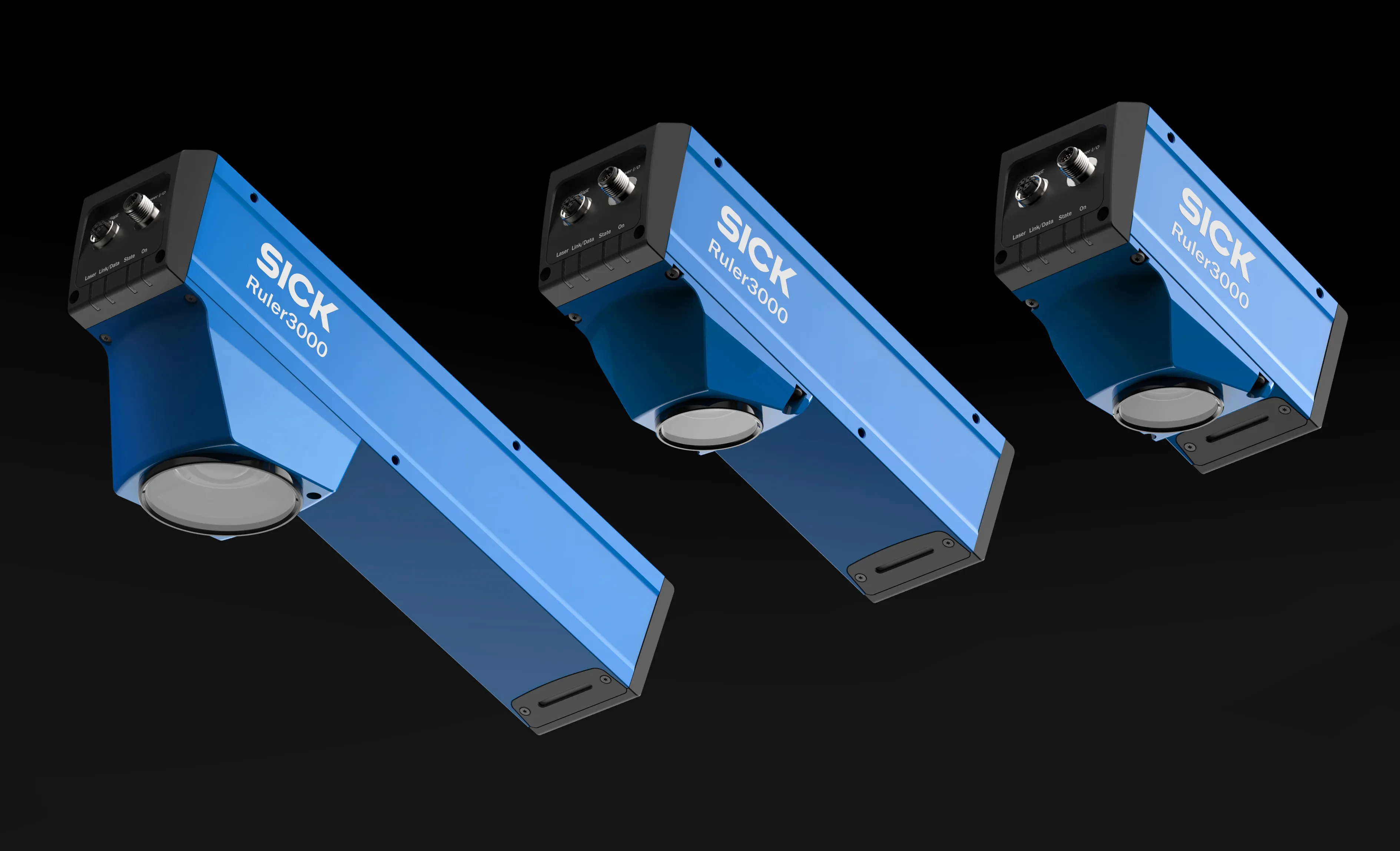
In this example of a family of 3D vision systems, two DFM elements stand out in particular:
- The modular design: The plug connection area and the opposite laser output are identical for different sizes. The production of identical parts reduces costs.
- A hybrid housing concept: The larger housing part of the product is a cut-to-length extruded profile, which significantly reduces the overall processing time. The lens attachment is designed as a milled part.
Thinking from the end. This is what DFM and Circular Design have in common...
Making manufacturing issues the starting point for product development has parallels with another trend that is increasingly influencing all product designs today and also has its origins in the 1970s. In 1972, the Club of Rome published its first report "The Limits to Growth". Many forecasts, e.g. about the scarcity of metals or fossil fuels, initially proved to be premature, as they were more than offset by the development of new deposits. But awareness of the finite nature of resources was awakened. And the images of the blue planet Earth from the Apollo program with its wafer-thin atmospheric shell changed the attitude from "everything can be solved technologically" to a view of natural processes that are characterized by the fact that they function as permanently closed cycles.
The need for permanently closed cycles was summarized in a book by W. McDonough and M. Braungart in 2002 (see graphic) and significantly promoted by the activities of the Allen Mac Arthur Foundation from 2012 onwards. It has now become a guiding principle of European policy.
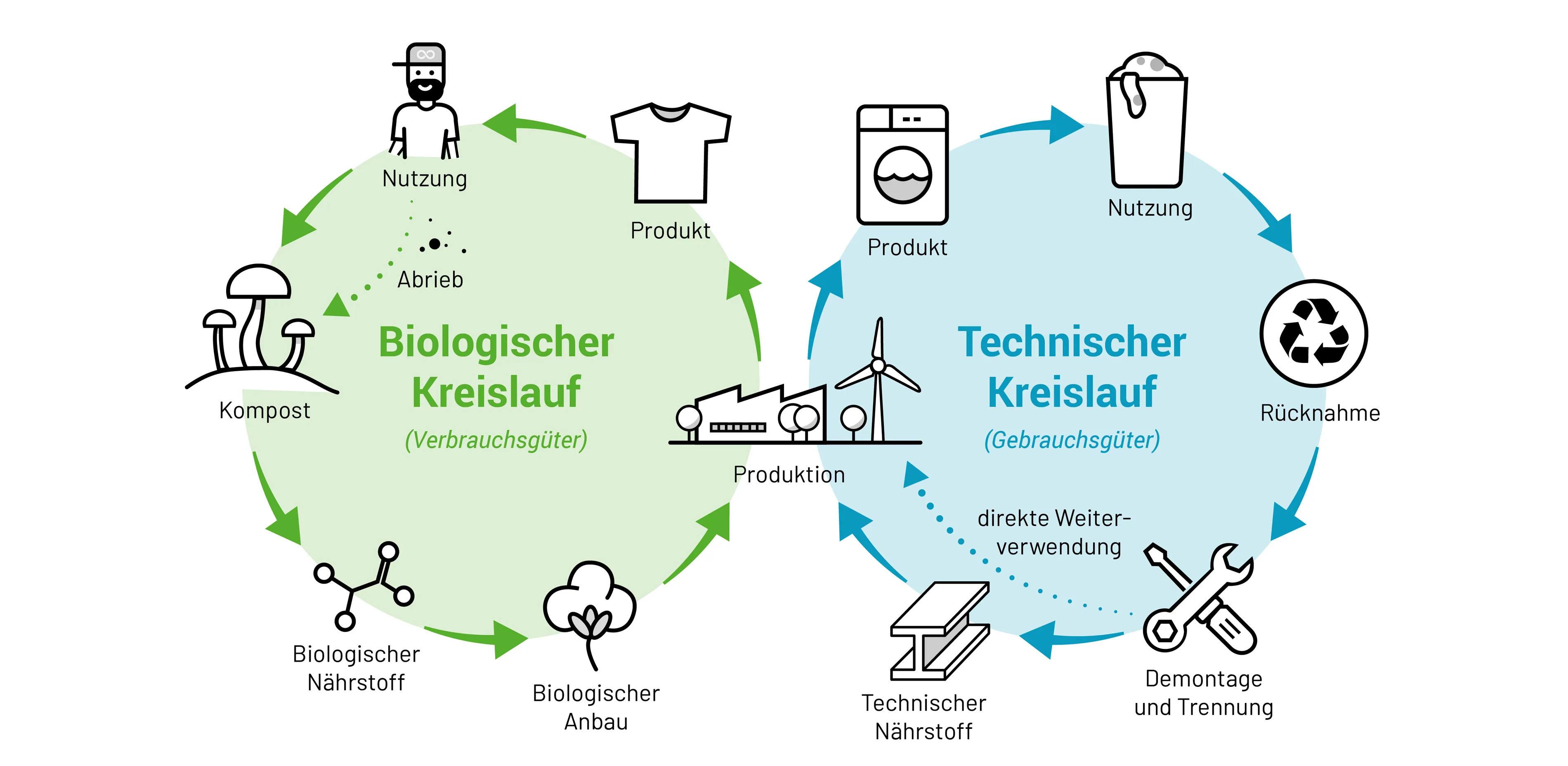
(Wikimedia: Felix Müller 2022)
In medical design, we are still at the very beginning of this development. Due to hygiene requirements, single-use products are very common. However, reusable alternatives for complex medical instruments are also becoming increasingly common. The remanufacturing of medical instruments is no longer just a phenomenon in emerging countries, but is also increasingly being practiced in developed economies. Hybrid concepts are becoming more and more popular, in which the technical components are reused hundreds of times and single-use only applies to those components that come into direct contact with the operating theater and therefore have to be sterile. Here, too, there are approaches for taking back and recycling these components in an organized manner.
It is clear that the circular economy will also become a defining factor in medical design. It is interesting to note that many DFM tactics also correspond to the goals of circular design. This means that we can kill two birds with one stone if we want to optimize production using DFM. User-centered design gives us the reason and motivation to develop the right product and DFM paired with Circular Design ensures that we develop it right. Circular Design, Design for Manufacturing and usability engineering in a professional development process is becoming a core competence for Next Gen Medical Design.
Author: Frank Detering, WILDDESIGN Stuttgart, 2023
04 Tips from the expert
- Think development from the end
Plan your product from the outset with a view to production and sustainability. This allows you to make optimal quality-defining decisions right from the start. - Rely on Design for Manufacturing to optimize costs
Reduce components and simplify assembly processes to cut production costs. Use the experience of your developers, as 80% of product costs are determined in the development phase. - Integrate circular design principles
Promote closed loops through material selection and product design. Develop reusable or recyclable products to conserve resources and promote sustainability. - Combine usability engineering, DFM and circular design
Think of these three approaches together to develop products that are user-friendly, efficient to manufacture and sustainable. This is becoming the core competence in Next-Gen Medical Design.
Frequently asked questions
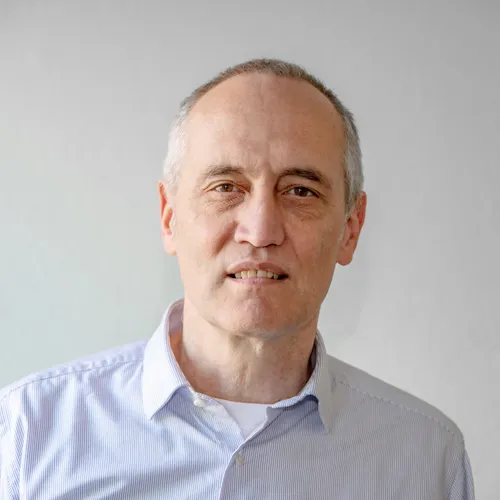