Perspective
5 reasons for DIY during the creative process
This article is currently only available in English.
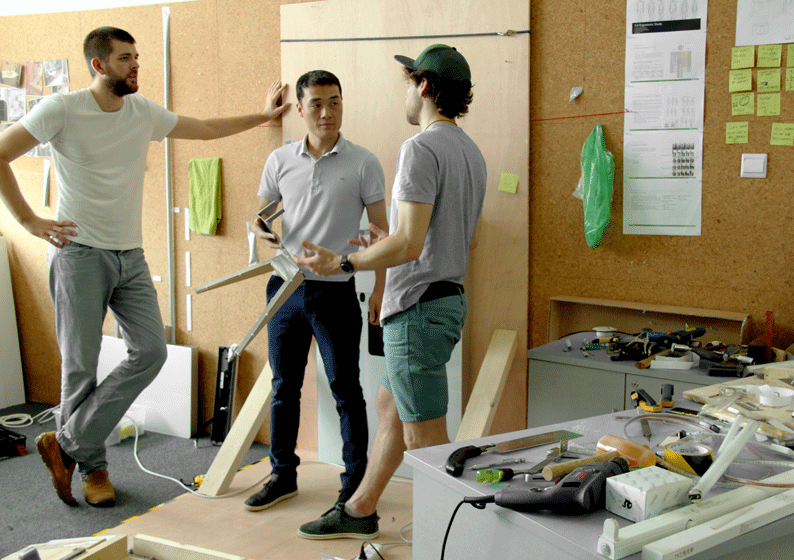
Our workshop has been a bit crowded these couple of weeks with mockups and projects everywhere. However, with prices so reasonable that even college students can hire them finding a handyman or model maker in Shanghai isn't too difficult. So why are our designers choosing to ditch the help and go at it DIY style? We interviewed a few of our busy bees and asked them just what motivates them to pick up their tools.
Manuel ARIAS
Graphic designer | Packaging
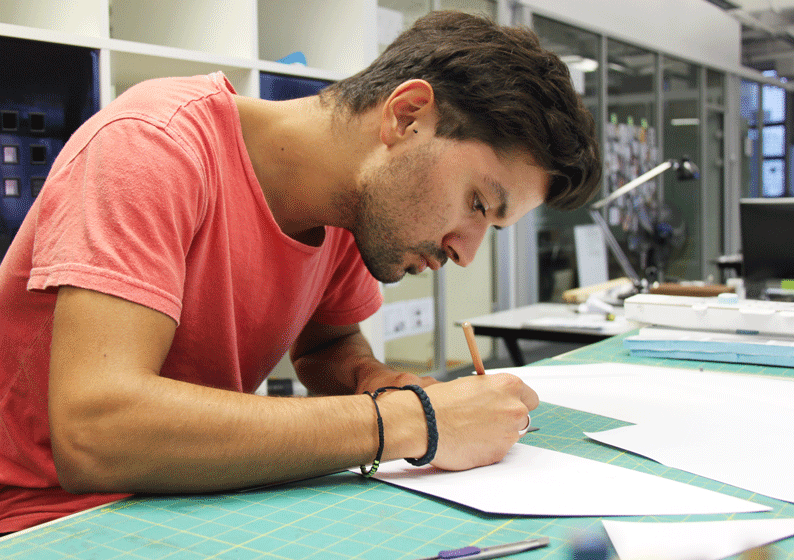
From a graphic design point of view making a mock-up is how we obtain ideas that will inspire us to create the packaging at the beginning of the design process. Therefore, during the sketching and brainstorming, generating real sized or proportional models is an efficient way to creatively play around and obtain insights on how to approach the visual solutions we aim for, since here not only visual aspects are important, but also the functionality and user interaction.
Just as we learn from our mistakes in life, that's how you also learn from mock-ups or 'dummies' in the design world. Through them you are able to correct any visual mistakes, unwanted outcomes and finally refine it until we reach the design quality and direction we were aiming for from the beginning. Put simply making mock ups gives us a greater control of the details and where there is good attention to detail, there will always be good design that follows.
Xiaodong MA
Product designer | Product
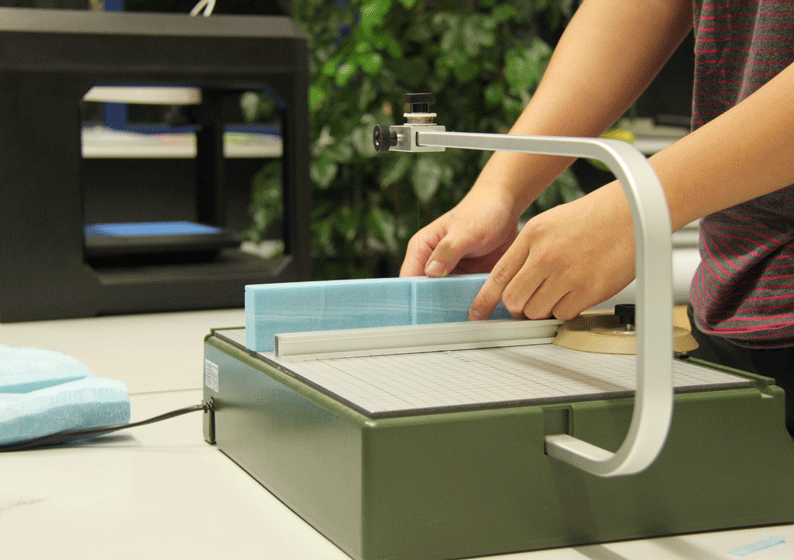
I think making mock-ups at the early stages of the concept phase is a relatively standard approach. It usually takes about 20 minutes for each mock-up at the initial concept stage. Creating a wide range of variations is more important than the quality at this stage. These mock-ups support our progress by bringing various concept sketches to a comparable level, making the assessment of the design easier and less subjective.
Modeling also inspires people to see the design differently in an immediate way as they add or remove pieces of material. For me, the most exciting thing about the DIY approach is that it helps give me a more sensory feeling of the design and gives me a more intimate overview of the product's features and ergonomics.
François DE MARTRIN-DONOS
Product designer | Product & User-Interface
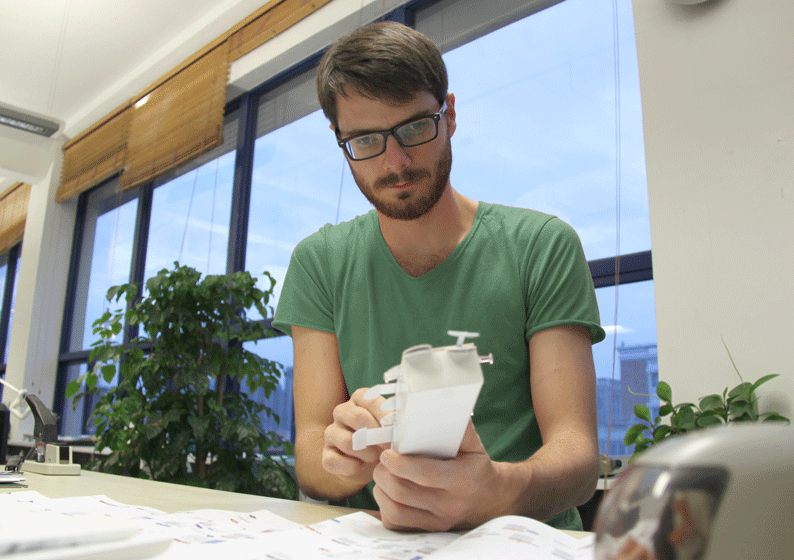
I recently used a DIY approach on a user interface project. In order to organize a workshop with potential users and gather feedback on the usage experience, we made quick models aiming to recreate several user interface concepts. By physically modelling the product from sketch, our team was able to validate design details and gain valuable insight into the most streamlined user experience.
Time was an important factor for us. Instead of wasting it refining a concept and discovering mistakes later on, we prefer to make rapid low-fidelity mock-ups that already give us a better understanding of the concept as well as useful feedback to adjust the user experience at an early phase.
Additionally doing more hands-on prototyping work gives us a welcome release from the sometimes limited digital world. It creates new approaches to the concept and brings new perspectives to the overall design process altogether. Indeed, by realizing a mock-up, a designer is able to get a fresh understanding of the existing concept.
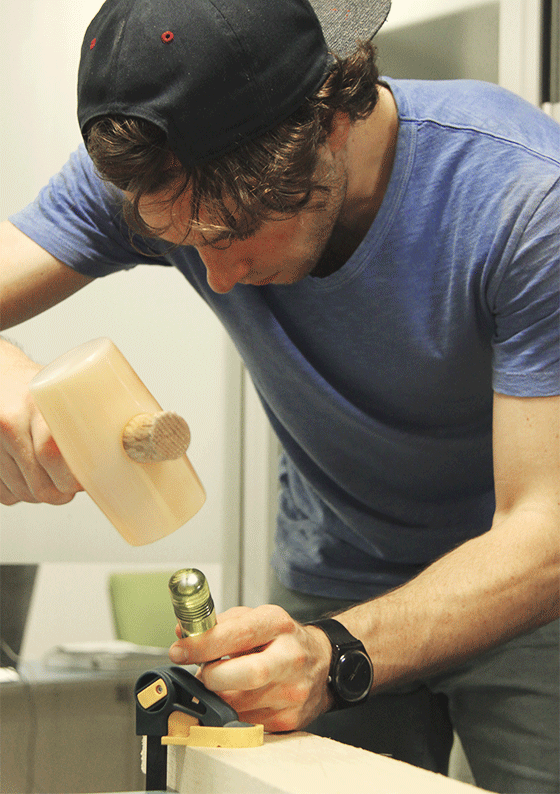
Jon WALMSLEY
Product designer | Interior & Product
What motivates me about model making is the process itself. You can't delete, paste or clone as if working on screen, you simply make mistakes, learn from them and scratch your head for a few seconds before you creatively stumble upon the solution. This process of iteration becomes more efficient over time with good preparation of materials and knowledge of replicating results using jigs and fixtures.
Working with raw materials that smell, splinter, crack and generally act unpredictably educates the designer in ways that no 3D modeling can. Over time, this narrative between both designer and material accumulates into a spectrum of knowledge which can then be applied during earlier phases of concept development using such frameworks as FMEA (Failure Modes Effects Analysis), ultimately providing more resolved solutions that reflect real scenarios during the products' use phase.
After a day of hard graft surrounded by tools, sawdust, the filings of metal and the odd cut or bruise, you look upon your creation and it stirs a sense of achievement similar to that of taking your first school design project home to your parents. Pride, which now hides behind a mask of objectivity and imminent concept refinement, for tomorrow you must allow for the critique of your team since you as a designer implore the iterative process.
Muhan Zhang
Product designer | Product
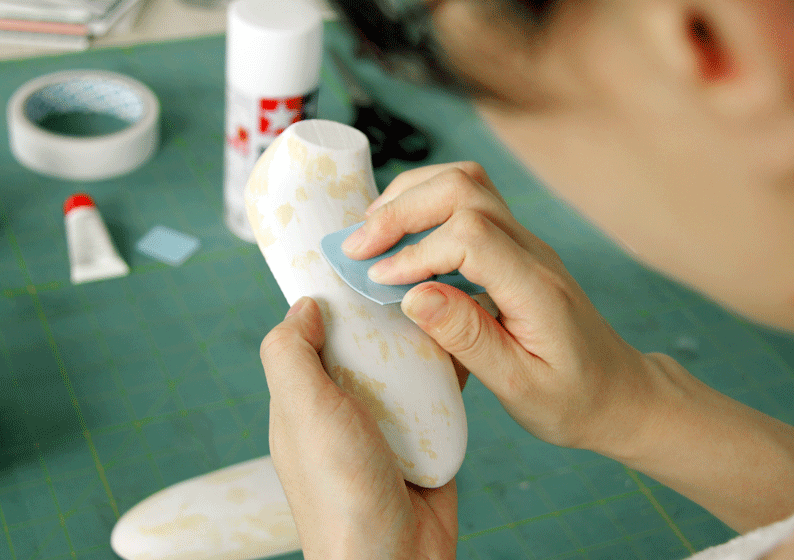
A pilot prototyping has a high fidelity to the final design which is used as a final check to tweak details before launching at scale. Based on the rapid prototyping made with the 3D printer, making a pilot prototyping has become a quick method to deliberate and adjust the aesthetics. Every visible change of the surface, edge or "bone-line" is related to the final appearance. I prefer to do a pilot model myself because I want to take the chance at the very last stage to refine my design.
In addition, I think the pilot model supports the communication very well. It's quite helpful when we discuss parting lines, painting sections etc. with our client. At the same time it's a good reference for the manufacturer when we hand over our design to them while also use it to collect feedback from professional salesman about potential economic attractiveness.
Frequently asked questions