Expertise
Quality awareness meets design culture: WILDDESIGN trains the entire team in quality management
The development of medical devices is no longer just about functioning technology - it's about responsibility. For patients, users and our customers. That's why at WILDDESIGN, design quality and regulatory safety go hand in hand and support each other - they are two sides of the same coin, so to speak. Living this requires more than just processes - it requires a shared understanding.
On July 8, the entire WILDDESIGN team came together once again in Gelsenkirchen to discuss the basics and subtleties of quality management (QM) in the design process with Dr. Marian Gransow (VIVE-MedTech). We regularly hold such events to deepen and refresh our knowledge and develop it further together.
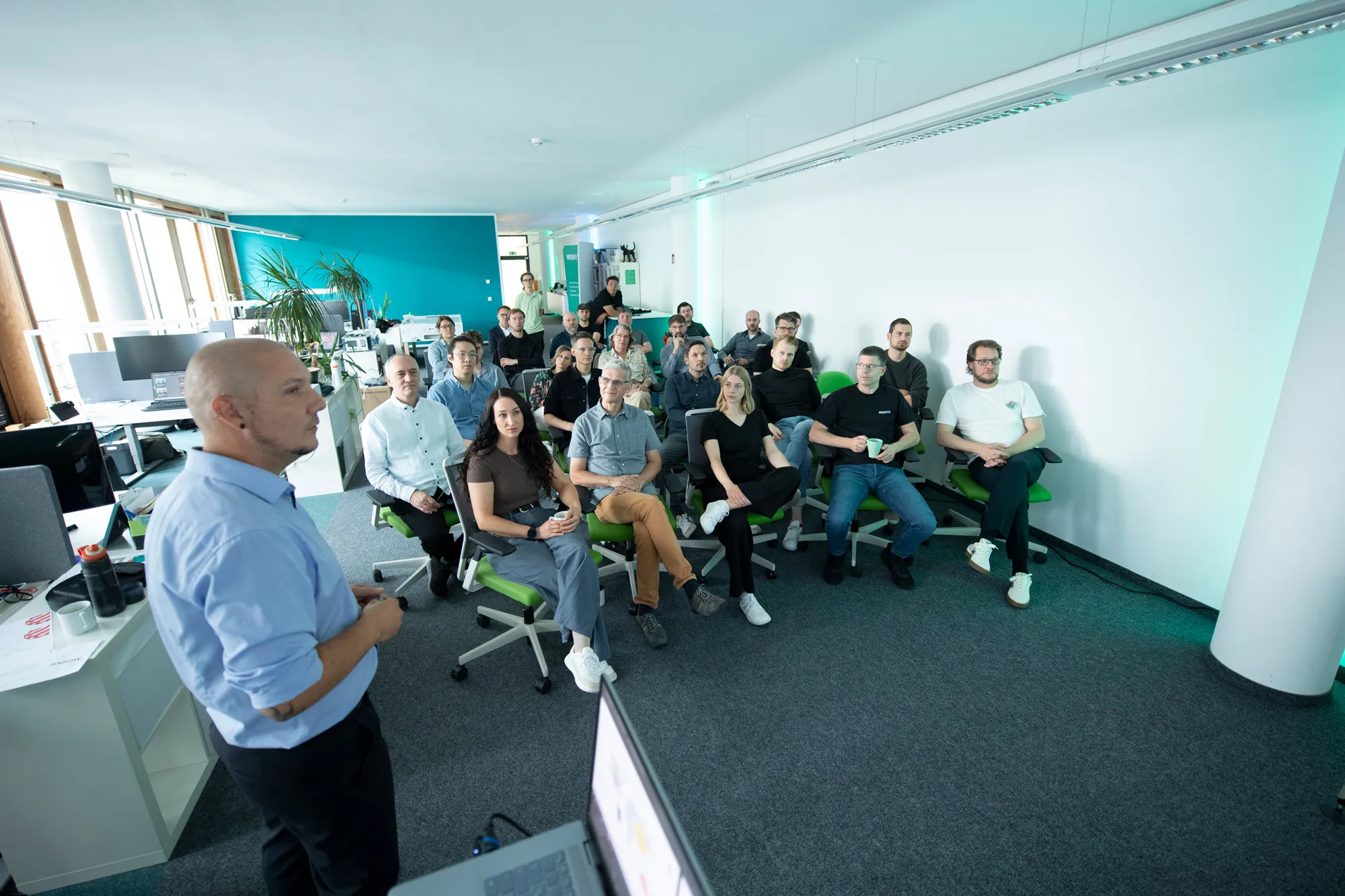
Quality management as part of the understanding of design
High normative requirements apply in medical technology - and rightly so. Dealing with risks, the traceability of decisions and complete documentation are not options, but a necessary basis for safe, marketable products. At the same time, the concept of quality in medical device development is changing: away from bureaucratic control and towards an active design instrument.
WILDDESIGN therefore consciously integrates QM into the medical design process - in other words, into the way we develop user-centered, innovative and regulatory-compliant products. Our customers value precisely this connection: creative ideas that are viable in a regulatory context. For this to succeed, our teams need a common understanding - and an intuitive QM system that harmonizes with daily project practice.
Learning in the context of real projects
The current training course was deliberately designed with a practical focus: After a compact refresher of the basics - particularly in relation to our interfaces with the customer - we presented the updates to our internal quality management system in Confluence. The aim was to enable all team members to understand this system as an integral part of their daily project work and to use it confidently. The focus was not only on documentation routines, but also on requirements for usability engineering and mechanical product safety - such as stability, tilt resistance and robust construction. What requirements apply? What evidence do we need? How do we communicate risks and decisions transparently?
A central component was the joint reality check in the group: we analyzed a specific project from the recent past. How did it work? What decisions were made - and how would our internal QMS have supported or changed this process today? This format brought theory and practice together and created the necessary transfer.
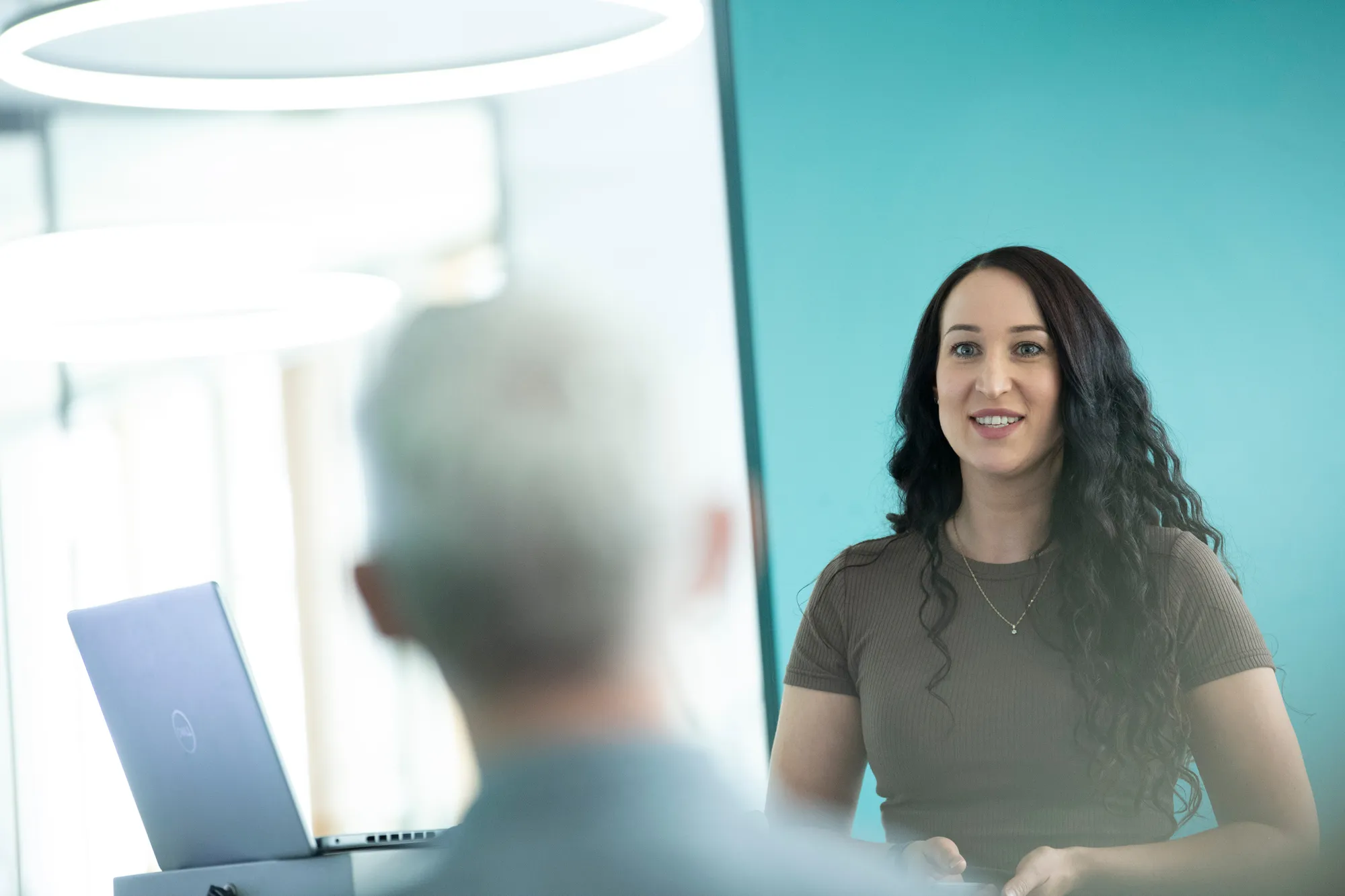
Design is responsibility - and quality is a promise
In times of increasing regulatory complexity, the design process becomes the decisive bridge between ideas and market maturity. Our aim is to design safe, functional and inspiring products together with our customers - whether for operating theaters, intensive care units, surgeries or homecare.
The regular training of our team is a building block of this claim. They ensure that we work with a common understanding of quality across locations and disciplines. Because we believe that quality is not created through control alone - it is created through dialog, attitude and responsibility in the project.
Frequently asked questions
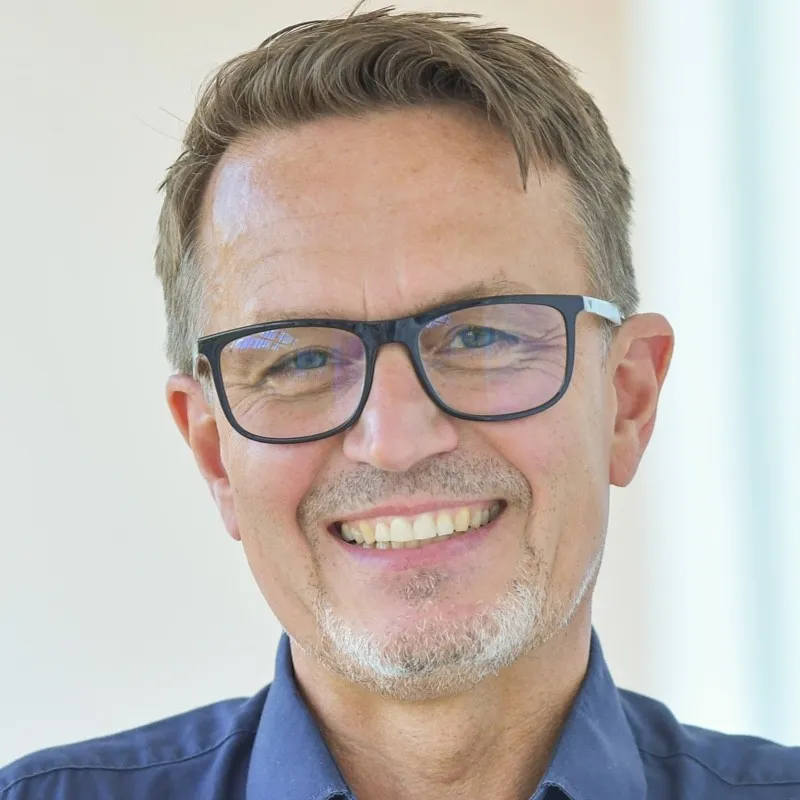